tvr plenum testing
-
- Posts: 954
- Joined: Wed Feb 16, 2011 5:12 am
- Location: oxford ,england .
Re: tvr plenum testing
Ah in this instance tony i have a valve that block one side till I get to the boost required then it opens to give both ports the goods.
medusa assembled..first drive
https://www.youtube.com/watch?v=zKMvQQm7Cn4&t=5s
https://www.youtube.com/watch?v=zKMvQQm7Cn4&t=5s
-
- Posts: 1452
- Joined: Wed Mar 03, 2010 3:40 pm
- Location: Melbourne, Australia
Re: tvr plenum testing
Yes exactly.
That is how my experimental system was set up too.
That is how my experimental system was set up too.
Also known as the infamous "Warpspeed" on some other Forums.
-
- Posts: 954
- Joined: Wed Feb 16, 2011 5:12 am
- Location: oxford ,england .
Re: tvr plenum testing
ah i see ,so you had v high back pressure until the port opened than normal back pressure ,but the high back pressure with the port closed made the higher boost before the opening of the port useless,is that what you mean?
what size engine and what turbo tony?
what size engine and what turbo tony?
medusa assembled..first drive
https://www.youtube.com/watch?v=zKMvQQm7Cn4&t=5s
https://www.youtube.com/watch?v=zKMvQQm7Cn4&t=5s
-
- Posts: 1452
- Joined: Wed Mar 03, 2010 3:40 pm
- Location: Melbourne, Australia
Re: tvr plenum testing
Engine size 1.6 litres DOHC four valve, overlap 25 degrees.
Turbo was a now ancient T3 sleeve bearing Garrett, with split pulse .83 exhaust, but it is all there was 35 years ago.
Back in those days the more efficient ball bearing turbos had not yet been invented.
Half the dual scroll was blocked off with a wastegate producing an A/R of something like .42
The idea was, when full initial boost arrived, the wastegate would bleed off excess exhaust into the second side of the scroll, which also had its own wastegate set to slightly higher final boost pressure.
What happened is the turbine inlet pressure became so very high, the exhaust reversion was massive, and the engine just choked to death. It was definitely not an improvement.
I was not the very first to try this, and I occasionally hear others have tried this idea since.
As it has not now become a widely popular demon tweak, I can only assume that the whole idea is a dud.
What definitely does work, and what I still get very excited about is placing a roots blower between turbo and engine.
There are no disadvantages, If you can figure a way to get it all in there.
Turbo was a now ancient T3 sleeve bearing Garrett, with split pulse .83 exhaust, but it is all there was 35 years ago.
Back in those days the more efficient ball bearing turbos had not yet been invented.
Half the dual scroll was blocked off with a wastegate producing an A/R of something like .42
The idea was, when full initial boost arrived, the wastegate would bleed off excess exhaust into the second side of the scroll, which also had its own wastegate set to slightly higher final boost pressure.
What happened is the turbine inlet pressure became so very high, the exhaust reversion was massive, and the engine just choked to death. It was definitely not an improvement.
I was not the very first to try this, and I occasionally hear others have tried this idea since.
As it has not now become a widely popular demon tweak, I can only assume that the whole idea is a dud.
What definitely does work, and what I still get very excited about is placing a roots blower between turbo and engine.
There are no disadvantages, If you can figure a way to get it all in there.
Also known as the infamous "Warpspeed" on some other Forums.
-
- Posts: 954
- Joined: Wed Feb 16, 2011 5:12 am
- Location: oxford ,england .
Re: tvr plenum testing
there are a fair few people out there selling and using a spool valve like i have ,and its working well in the right situation , the key seems to be that the valve is big enough to pass all the gas into the 2nd side ,maybe the wastegate was not flowing enough ?
anyrdup , my main thing was to see if the new hx50 was going to spool faster than the old hc3 ,and thank god i did the test rather than bung it on and have to make loads of plates n fitments ...because its almost the same and not much of an improvement at all!
now i have the dillema of whether to use the hx40 16cm or the 19cm turbine housing . i am tending towards the 19 with the spool valve , but i do like a bit of instantaneous boost.
even with the super small IHI it made 250 bhp @4500 (rolling road limit) and 296 lbs/ft on only 9 psi with no air flowing through the intercooler . on 12 psi ,with more fuel, it felt pretty rapid and would run best possible of 12,32 1/4 mile ...on treaded tyres .in 1993!!
anyrdup , my main thing was to see if the new hx50 was going to spool faster than the old hc3 ,and thank god i did the test rather than bung it on and have to make loads of plates n fitments ...because its almost the same and not much of an improvement at all!
now i have the dillema of whether to use the hx40 16cm or the 19cm turbine housing . i am tending towards the 19 with the spool valve , but i do like a bit of instantaneous boost.
even with the super small IHI it made 250 bhp @4500 (rolling road limit) and 296 lbs/ft on only 9 psi with no air flowing through the intercooler . on 12 psi ,with more fuel, it felt pretty rapid and would run best possible of 12,32 1/4 mile ...on treaded tyres .in 1993!!
medusa assembled..first drive
https://www.youtube.com/watch?v=zKMvQQm7Cn4&t=5s
https://www.youtube.com/watch?v=zKMvQQm7Cn4&t=5s
-
- Posts: 1452
- Joined: Wed Mar 03, 2010 3:40 pm
- Location: Melbourne, Australia
Re: tvr plenum testing
Spool valve size was not my problem, it was a 42mm flow Garrett wastegate..
The problem was trying to flow all the exhaust through about a 20mm hole with about 0.4 A/R.
It was just far too small.
The problem was trying to flow all the exhaust through about a 20mm hole with about 0.4 A/R.
It was just far too small.
Also known as the infamous "Warpspeed" on some other Forums.
-
- Posts: 954
- Joined: Wed Feb 16, 2011 5:12 am
- Location: oxford ,england .
Re: tvr plenum testing
it just occurred to me , i wonder if i can predict the hx40 spool characteristics from this data .
eg , from this
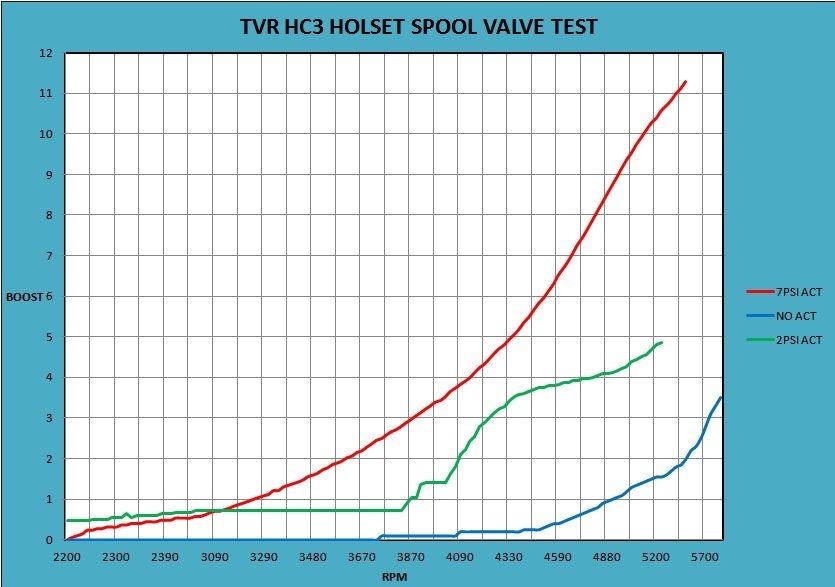
we can see the difference at 4k rpm is 4 psi with the spool valve shut ,and just starting to boost with it open .so a difference of 4 psi.
looking at the flow bench graph,
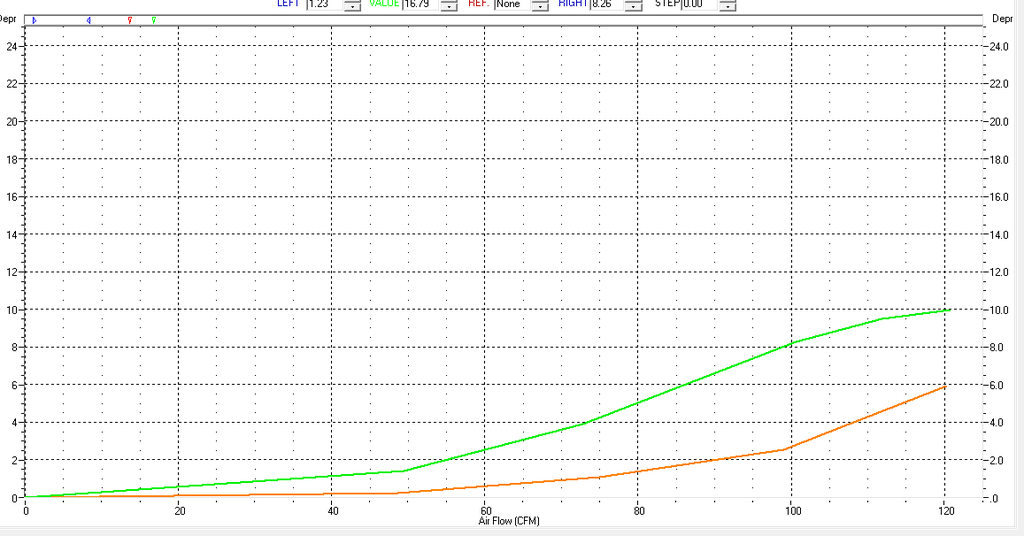
this is the hc3 open and closed ,we can see the differences in flow and boost .and ,on average the pressure is doubled with the port shut .
now if i plot the hx40 on there ..
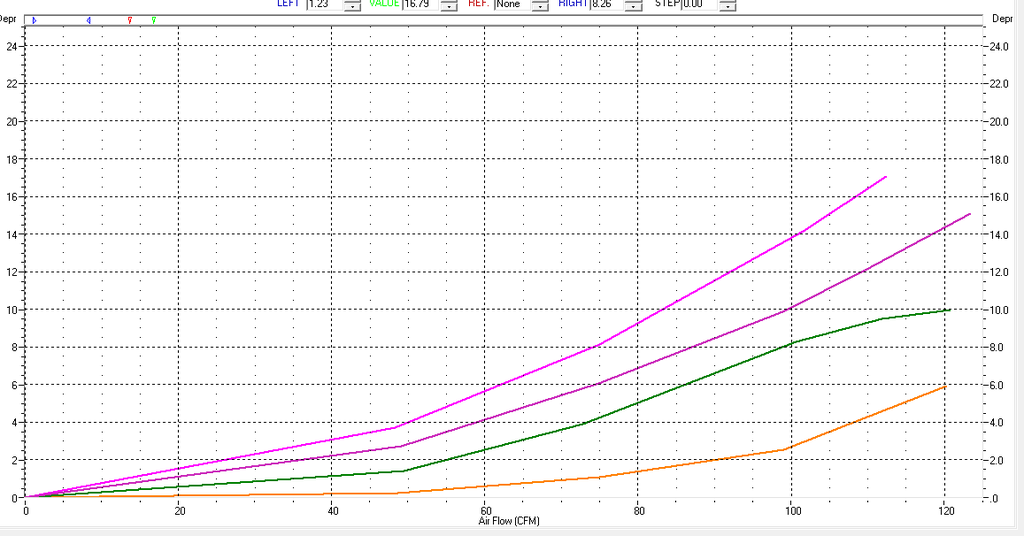
that's the open 19cm and 16cm housings ,we can see the improvement in response .
the 19 cm doesn't seems a lot better , but the 16cm does .
now the q is , can i take say the ported hc3 ,at 10"@100 cfm and look back horizontally to see where the the others achieve at that figure of 10" eg 86 and 75 cfm ,and say ok that's a percentage of the 100cfm hc3 figure ,....can i just take that off the rpm of the logged boost curve?
so 4 psi @4000rpm becomes 4 psi @3440 or @3000rpm.
taking it a step further..
the spool valve closed versions of the 19cm and 16 cm ,versus the closed hc3
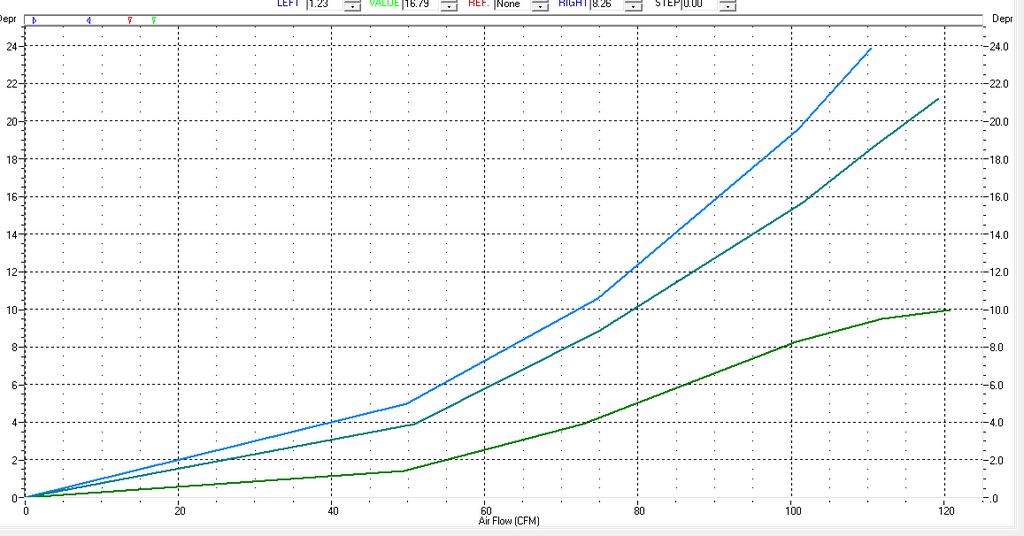
would give us , instead of 4 psi@4000 rpm ,4 psi@2840 rpm ,and @ 2520 rpm .
of course ,another way to approach it would be to say ,ok at 5k rpm on the log ,the ported is 9 psi approx over the unported ,if the hx 40 ported 19cm is more than double the difference between the hc3 open and closed , is it then going to make more than double the difference in boost ,so over 18 psi at 5k?
the above is probably total drivel and nonsense , but there must be some correlation?
regards
robert
eg , from this
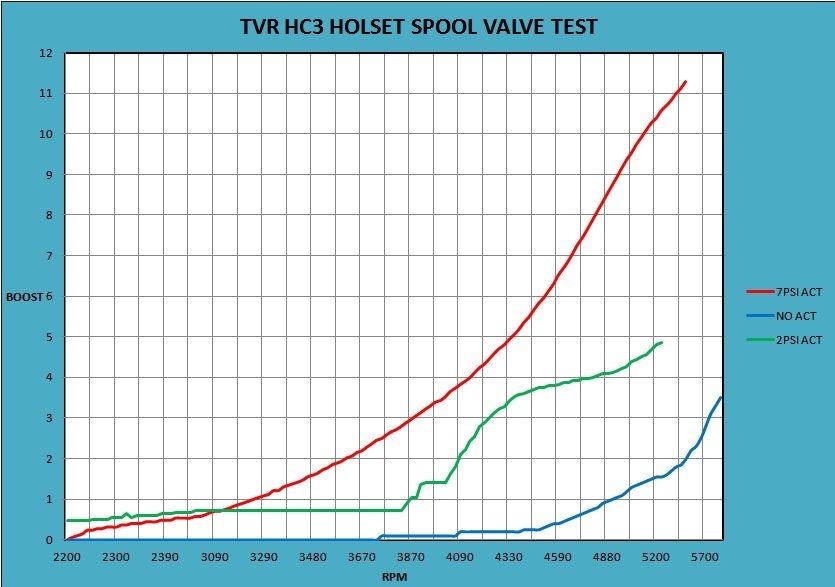
we can see the difference at 4k rpm is 4 psi with the spool valve shut ,and just starting to boost with it open .so a difference of 4 psi.
looking at the flow bench graph,
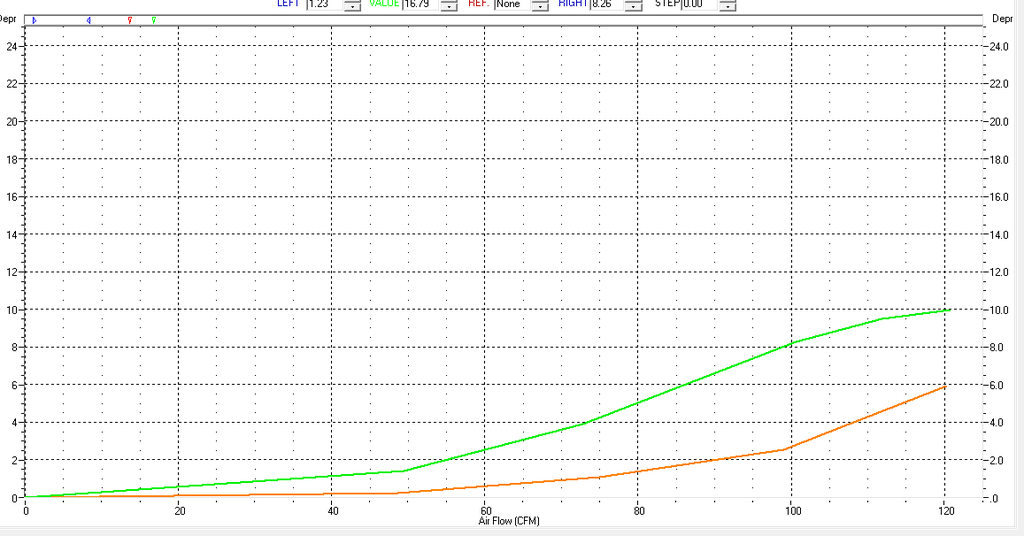
this is the hc3 open and closed ,we can see the differences in flow and boost .and ,on average the pressure is doubled with the port shut .
now if i plot the hx40 on there ..
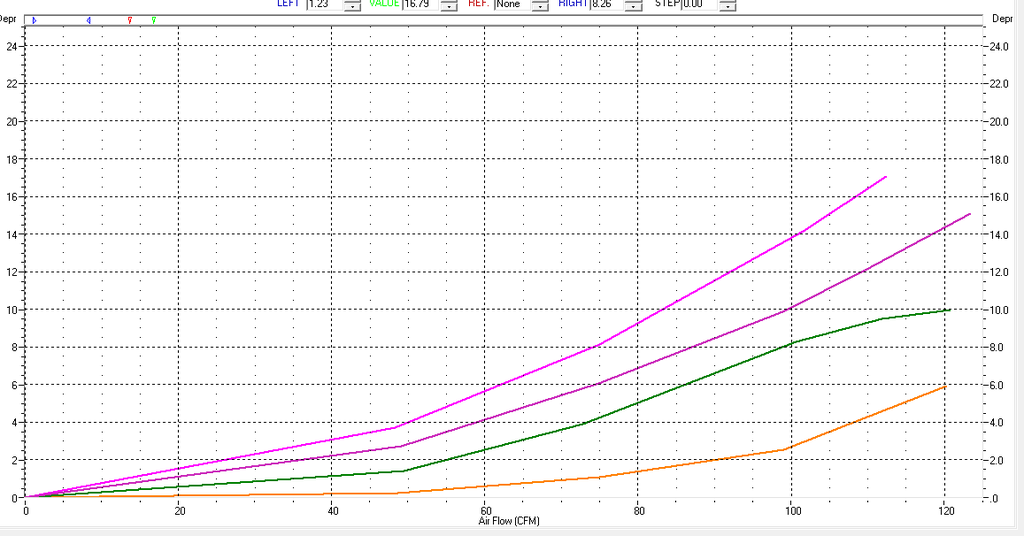
that's the open 19cm and 16cm housings ,we can see the improvement in response .
the 19 cm doesn't seems a lot better , but the 16cm does .
now the q is , can i take say the ported hc3 ,at 10"@100 cfm and look back horizontally to see where the the others achieve at that figure of 10" eg 86 and 75 cfm ,and say ok that's a percentage of the 100cfm hc3 figure ,....can i just take that off the rpm of the logged boost curve?
so 4 psi @4000rpm becomes 4 psi @3440 or @3000rpm.
taking it a step further..
the spool valve closed versions of the 19cm and 16 cm ,versus the closed hc3
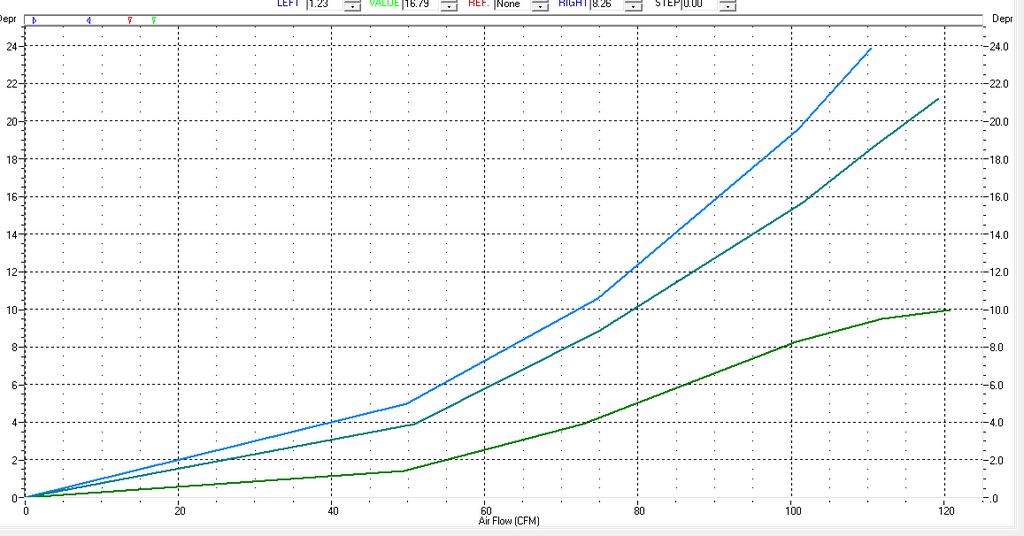
would give us , instead of 4 psi@4000 rpm ,4 psi@2840 rpm ,and @ 2520 rpm .
of course ,another way to approach it would be to say ,ok at 5k rpm on the log ,the ported is 9 psi approx over the unported ,if the hx 40 ported 19cm is more than double the difference between the hc3 open and closed , is it then going to make more than double the difference in boost ,so over 18 psi at 5k?
the above is probably total drivel and nonsense , but there must be some correlation?
regards
robert
medusa assembled..first drive
https://www.youtube.com/watch?v=zKMvQQm7Cn4&t=5s
https://www.youtube.com/watch?v=zKMvQQm7Cn4&t=5s
-
- Posts: 1452
- Joined: Wed Mar 03, 2010 3:40 pm
- Location: Melbourne, Australia
Re: tvr plenum testing
Robert, your pictures are not showing.
A lot depends on how well your engine accepts high exhaust back pressure.
Its not correct to just assume that fitting a smaller and smaller turbine a/r creates more and more low end boost.
Try to imagine what happens if you fit a turbine housing with a 1mm hole.
You are not going to see 10 psi boost at engine idle.
There is some minimum flow area that works on a particular engine, and choking it off any further is not productive.
In my experience you would be much better off just using a well matched "latest technology" high dollar ball bearing turbo.
A lot depends on how well your engine accepts high exhaust back pressure.
Its not correct to just assume that fitting a smaller and smaller turbine a/r creates more and more low end boost.
Try to imagine what happens if you fit a turbine housing with a 1mm hole.
You are not going to see 10 psi boost at engine idle.
There is some minimum flow area that works on a particular engine, and choking it off any further is not productive.
In my experience you would be much better off just using a well matched "latest technology" high dollar ball bearing turbo.
Also known as the infamous "Warpspeed" on some other Forums.
-
- Posts: 954
- Joined: Wed Feb 16, 2011 5:12 am
- Location: oxford ,england .
Re: tvr plenum testing
that's a microsoft answer tony
technically accurate , but of no practical use to me with no money lol.
here's a good bit on the housings .
http://turbolabofamerica.com/turbine-housings/
my housing is a 16cm , or as they put it a 1.13 a/r .that's too big for the response i want ,so it may work well with a valve ..as i always say ...TIME WILL TELL.
interesting thread on here ..
http://www.theturboforums.com/threads/2 ... more-boost
regards
robert


technically accurate , but of no practical use to me with no money lol.
here's a good bit on the housings .
http://turbolabofamerica.com/turbine-housings/
my housing is a 16cm , or as they put it a 1.13 a/r .that's too big for the response i want ,so it may work well with a valve ..as i always say ...TIME WILL TELL.
interesting thread on here ..
http://www.theturboforums.com/threads/2 ... more-boost
regards
robert

medusa assembled..first drive
https://www.youtube.com/watch?v=zKMvQQm7Cn4&t=5s
https://www.youtube.com/watch?v=zKMvQQm7Cn4&t=5s
-
- Posts: 1452
- Joined: Wed Mar 03, 2010 3:40 pm
- Location: Melbourne, Australia
Re: tvr plenum testing
Just a thought, but consider the financial and engineering resources available to Honda Engineering.
They built the successful Honda TAG Formula One race engine, which was a winner (if it lasted the race).
It used a pair of variable vane turbos of Honda’s own unique in house design.
Honda marketing and management all fired up by their Formula One engine development success, and the publicity it generated, decided the very same variable vane turbo technology should be applied to their top of the range Honda road production car.
http://dwolsten.tripod.com/articles/jan89a.html
Guess what, it did not work.
It must have been a huge loss of face to the Honda engineers, after Honda management promised so much.
Why did it not work ?
Variable vane turbos work great on unthrottled diesels.
The answer lies in the fact that excessive exhaust back pressure strangles the engine.
Now an amateur home tuner may be extremely happy with any result that is just better than truly awful.
But professional engineers are a bit more enquiring and demanding.
Do you really believe that some of the the finest automotive engineers in the world backed by the huge financial resources of multinational corporations, including the engineers from Garret, KKK, Holset, IHI and other turbo manufacturers never thought of this simple idea ?
Garret manufacture millions of variable vane turbos for diesels, but they know quite well that a decent well matched fixed turbine housing ball bearing turbo will beat a variable vane turbo on a throttled petrol engine.
So they mass produce both types. Both are superior in their own specific field of application.
The apologists say the vanes die from heat, but that is simply not true. Turbine vanes are made from the same material as the turbine blades. Or the other excuse, movable vane mechanism jams from lead deposits. Maybe true before unleaded petrol, not today.
Been there done all this myself a very long time ago.
The fact I could not make it work after tying for eighteen months is not remarkable.
The fact that none of the turbo manufacturers could make it work either is worthy of note.
Only Porsche persisted and came up with a hugely complex system that arguably might have worked just as well with something a lot simpler.
They built the successful Honda TAG Formula One race engine, which was a winner (if it lasted the race).
It used a pair of variable vane turbos of Honda’s own unique in house design.
Honda marketing and management all fired up by their Formula One engine development success, and the publicity it generated, decided the very same variable vane turbo technology should be applied to their top of the range Honda road production car.
http://dwolsten.tripod.com/articles/jan89a.html
Guess what, it did not work.
It must have been a huge loss of face to the Honda engineers, after Honda management promised so much.
Why did it not work ?
Variable vane turbos work great on unthrottled diesels.
The answer lies in the fact that excessive exhaust back pressure strangles the engine.
Now an amateur home tuner may be extremely happy with any result that is just better than truly awful.
But professional engineers are a bit more enquiring and demanding.
Do you really believe that some of the the finest automotive engineers in the world backed by the huge financial resources of multinational corporations, including the engineers from Garret, KKK, Holset, IHI and other turbo manufacturers never thought of this simple idea ?
Garret manufacture millions of variable vane turbos for diesels, but they know quite well that a decent well matched fixed turbine housing ball bearing turbo will beat a variable vane turbo on a throttled petrol engine.
So they mass produce both types. Both are superior in their own specific field of application.
The apologists say the vanes die from heat, but that is simply not true. Turbine vanes are made from the same material as the turbine blades. Or the other excuse, movable vane mechanism jams from lead deposits. Maybe true before unleaded petrol, not today.
Been there done all this myself a very long time ago.
The fact I could not make it work after tying for eighteen months is not remarkable.
The fact that none of the turbo manufacturers could make it work either is worthy of note.
Only Porsche persisted and came up with a hugely complex system that arguably might have worked just as well with something a lot simpler.
Also known as the infamous "Warpspeed" on some other Forums.